TL;DR: I made a lithophane lamp shade for my sister’s birthday. I used an online tool that combined multiple images with specific measurements to create a part that fit around my particular desk lamp. This was probably my longest single part print to date—about 60 hours, but the results were well worth the wait!
I continued playing around with lithophanes and made my sister a birthday present—a litphophane lamp shade! I found another online tool at: https://www.lithophanemaker.com/Lamp%20Lithophane.html. This one lets you enter various parameters to create an entire ready-to-print part very quickly. While I would design this part a bit differently if I were to do it from scratch, the speed of use was pretty undeniable.
I only had a two small hiccups—the size of the lamp retaining lip didn’t quite match what I expected. That is—the cylinder turned out undersized for what I needed. Luckily, I had the foresight to first print only the inner cylinder for a fit check. After I started the print the first time, I realized that I forgot to add supports for the cylinder retaining lip to come out properly, so I had to restart the print after a few hours >.<.
Once I started the print for real, I had the full lamp shade in hand after about 60 hours. This was my longest single part print to date, and I think it turned out incredibly well 😀
The gallery with descriptions below shows the process:
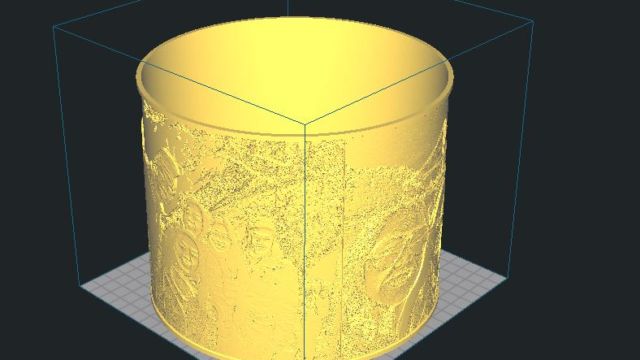
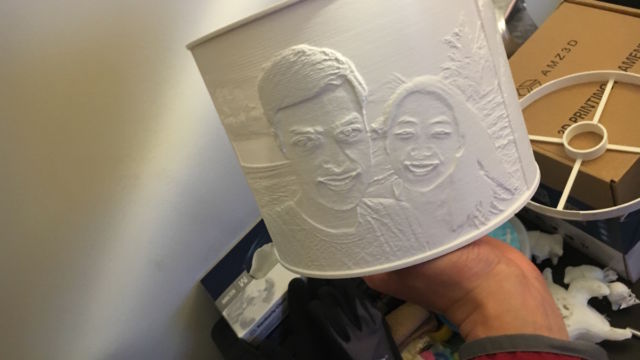